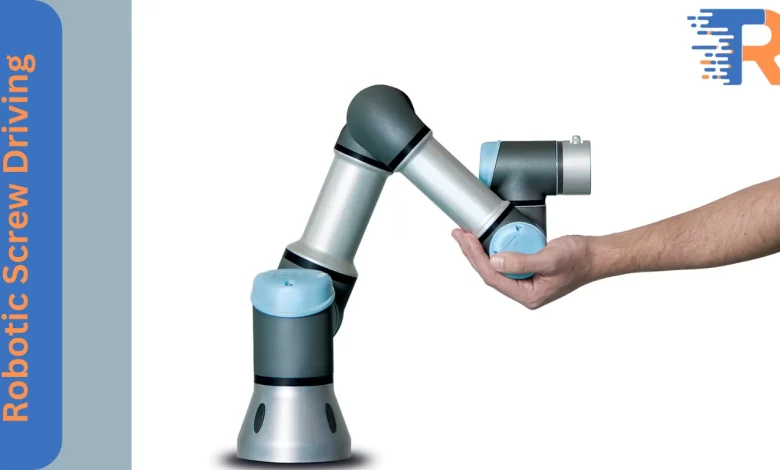
Robotic Screw Driving is a basic cycle in different ventures, empowering computerization, accuracy, and proficiency. As the assembling scene keeps on developing, understanding the complexities of automated drives and end effectors is fundamental. In this article, we will dig into the universe of automated screw driving, investigating the kinds of drives, the meaning of end effectors, and the various advantages and highlights of this imperative innovation.
What Are Robotic Drives?
Automated drives are the mechanical frameworks that power and control the development of robots. With regards to mechanical screw driving, drives assume a urgent part in directing the screwdriver to the ideal area, guaranteeing the right measure of force is applied, and accomplishing exact and reliable outcomes. There are different kinds of drives utilized in mechanical frameworks, each with its extraordinary attributes and applications.
Types of Drives in Robotics
- Pneumatic Drives: Pneumatic drives utilize packed air to control the development of automated parts. They are known for their speed and dependability, making them appropriate for rapid, redundant screw driving undertakings.
- Electric Drives: Electric drives are generally utilized in mechanical frameworks. They give exact control and are versatile to different screw driving applications. Electric drives can be additionally arranged into servo drives and stepper drives, each offering particular benefits.
- Hydraulic Drives: Water powered drives utilize compressed liquid to control automated developments. They are many times utilized in substantial modern applications where high force and power are required.
- Linear Drives: Linear drives are used for straight-line movements. They are integral in screw driving tasks that demand linear precision.
- Rotary Drives: Rotary drives are designed for rotational movement and are crucial in tasks where screws need to be fastened or unfastened with precise angles.
What Is the End Effector in Robotics?
The end effector, otherwise called the finish of-arm tooling (EOAT), is the part connected to the furthest limit of the robot’s arm or wrist. In mechanical screw driving, the end effector is the part liable for dealing with and controlling screws. It guarantees that the screws are gotten, put in the right area, and safely affixed. The plan of the end effector fluctuates in light of the particular necessities of the screw driving undertaking.
Types of End Effectors Used in Robotics
- Grippers: Grippers are a common type of end effector used in robotic screw driving. They have jaws or fingers that can grasp and hold screws securely. Grippers come in various sizes and designs to accommodate different screw sizes and shapes.
- Screwdrivers: Screwdriver end effectors are equipped with a motorized or pneumatic screwdriver tool. They can pick up screws, position them accurately, and apply the necessary torque for fastening.
- Magnetic End Effectors: Magnetic end effectors are used when handling ferrous screws. They utilize magnets to attract and secure the screws during the screw driving process.
- Vacuum End Effectors: Vacuum-based end effectors use suction to pick up screws and other small components. They are versatile and can handle a wide range of screw sizes and types.
- Nutrunners: Nutrunners are specialized end effectors used for fastening nuts and bolts. They provide precise torque control for securing threaded fasteners.
Benefits of Robotic Screw Driving
Robotic screw driving offers a range of advantages, making it an invaluable process in modern manufacturing:
- Precision: Robots can consistently and accurately position and fasten screws with minimal variation, ensuring high-quality products.
- Efficiency: Robotic screw driving is significantly faster than manual labor, leading to increased production output and reduced labor costs.
- Reliability: Robots work tirelessly without fatigue, reducing the likelihood of errors or inconsistencies in screw driving tasks.
- Safety: By automating repetitive and potentially hazardous tasks, robotic screw driving enhances workplace safety.
- Flexibility: Robots can be reprogrammed and adapted to various screw driving applications, making them versatile assets in manufacturing.
Screw Driving Solutions and Features
When implementing robotic screw driving in your manufacturing process, it’s essential to consider the following solutions and features:
- Torque Control: Robotic screw driving systems should offer precise torque control to ensure screws are fastened to the correct specifications.
- Error Detection: Implementing sensors and error detection systems can identify issues in the screw driving process, such as missed or cross-threaded screws.
- Integration: Ensure your robotic screw driving system can seamlessly integrate with your existing manufacturing equipment and software.
- Programming and Ease of Use: User-friendly interfaces for programming and operating the robotic system are crucial for efficiency.
- Maintenance and Service: Choose systems with robust maintenance and service support to keep your robotic screw drivers operating at peak performance.
Conclusion
Mechanical screw driving is an innovation that consolidates the accuracy and effectiveness of robots with the flexibility of various drives and end effectors. It assumes a crucial part in present day fabricating, adding to the development of great items with speed and unwavering quality. Figuring out the kinds of drives, end effectors, and the various advantages and highlights of mechanical screw driving is fundamental for those hoping to embrace mechanization and upgrade their assembling processes. As innovation keeps on propelling, the job of mechanical screw driving in different businesses is ready for additional development, making it an essential piece of the computerization scene.
Explain 3 classify robot end effectors?
Here are three common classifications of robot end effectors:
- Grippers:
– Grippers are end effectors designed to grasp and hold objects securely. They come in various shapes and sizes to accommodate different objects.
– Grippers can be further classified into types like parallel grippers, which have two parallel jaws that move towards each other to grip an object, and angular grippers, which use angular motion to grasp objects from the sides.
– Grippers are versatile and commonly used in pick-and-place tasks, assembly, and material handling.
- Tools and Attachments:
– Some robots are equipped with specialized tools and attachments as end effectors. These can include items like welding torches, cutting blades, drills, and paint sprayers.
– These end effectors are tailored to perform specific tasks, such as welding, cutting, drilling, or painting.
– The choice of tool or attachment depends on the robot’s application, allowing it to execute precise and specialized functions.
- Suction Cups and Vacuum End Effectors:
– Suction cups and vacuum-based end effectors use suction to grip and manipulate objects. They are particularly useful for handling items with smooth or flat surfaces.
– Suction cups can vary in size and shape, and they are often used in applications such as pick-and-place tasks, packaging, and material handling.
– Vacuum end effectors offer flexibility when dealing with objects of different sizes and shapes, as the vacuum can conform to the object’s surface.
These characterizations address only a couple of the many sorts of end effectors accessible in mechanical technology. The decision of end effector relies upon the particular assignments the robot needs to perform and the sort of articles it will deal with.