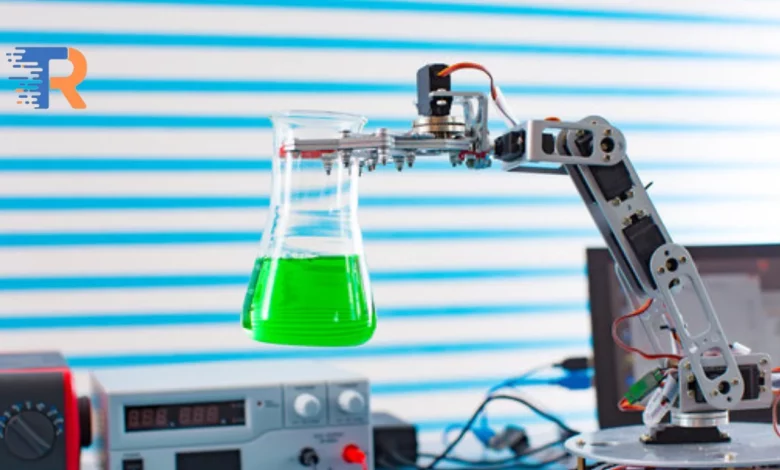
7 Reasons to Use-Robotics in Chemical Industry
-
Navigating Hazardous Terrain
An undeniable advantage of deploying robots in specific tasks lies in mitigating the perilous conditions faced by human workers. Nowhere is this more crucial than in the chemical industry, where a spectrum of tasks carries inherent risks.
Moreover, robots play a pivotal role in diminishing the frequency with which individuals need to don Personal Protective Equipment (PPE). This dual benefit not only enhances safety but also translates into time savings, amplifying overall task efficiency.
-
Crafting a Symphony of Uniformity
At the heart of robotic integration is the orchestration of unparalleled consistency in tasks. While human work may inherently fluctuate, a robot performs each task with unwavering precision, ensuring a symphony of uniformity.
In the intricate landscape of the Robotics in Chemical Industry, consistency emerges as a linchpin for crucial tasks such as measurement, chemical dispensing, and testing. The reliability that robots bring to these processes not only minimizes the margin for error but also sets the stage for elevated precision and reliability in every orchestrated task.
Must Read : COMMON TESTS IN AUTOMATED MACHINERY USE
-
Mastering the Toxic Tango
In the intricate ballet of chemical handling, robots emerge as virtuosos capable of effortlessly navigating the realm of toxic materials and chemicals. Unlike their human counterparts, robots, once shielded with appropriate safeguards, execute operations with minimal risk to people.
Consider, for instance, the protective embrace of sleeving, an armor for robots dealing with substances like paint and flammable liquids. This innovation exemplifies the symbiotic relationship between technology and safety, transforming potentially hazardous tasks into a seamless and secure operation.
-
Catalyzing Task Efficiency
In the Robotics in Chemical Industry, some tasks bear the inefficiencies inherent in human execution. Safety precautions, while essential, often introduce time-consuming steps that contribute little value to the core task. Robotics in Chemical Industry, Enter robots, poised to revolutionize productivity by streamlining processes and eliminating redundant safety measures.
The transformative potential lies not only in the initial gains but in the continuous refinement of robotic efficiency over time. Incremental improvements aggregate into substantial advancements, charting a course towards sustained productivity enhancements in the long run.
-
Eco-Friendly Precision Robotics in Chemical Industry
A burgeoning commitment to sustainability reverberates through the chemical industry, and robots stand as allies in the quest for reduced wastage. The consistent optimization of processes facilitated by robots becomes a linchpin in the drive towards both short-term and long-term sustainability.
Moreover, the error-reducing prowess of robots not only minimizes rework but also curtails wastage. This dual impact propels the industry towards a future where precision and sustainability intertwine seamlessly.
-
The Purity of Cleanroom Choreography
Navigating the stringent demands of cleanroom environments becomes a dance for robots designed for the task. Unlike their human counterparts, robots operating in cleanrooms don’t introduce contaminants, offering a pristine solution to a perennial challenge.
In the symphony of cleanroom working, Robotics in Chemical Industry become the guardians of purity. Freed from the risk of picking up contaminants from external sources, they redefine the standards of cleanliness, reducing contamination significantly and ensuring a harmonious interplay between technology and a pristine working environment.
-
Unleashing Uninterrupted Operations
In the dynamic landscape of automation, a standout advantage is the remarkable reduction of downtime achieved through the deployment of robots. Unlike their human counterparts, robots are devoid of the need for breaks, rendering them impeccable candidates for tasks demanding seamless continuity.
However, the key to unlocking this potential lies in selecting the optimal programming interface. Choosing the right interface becomes a crucial determinant in the quest to minimize downtime and amplify the efficiency of robotic operations. Dive deeper into this realm of efficiency with insights provided in our article, “10 Excellent Ways to Save Time with Offline Programming.”
Advantages
- Versatile Roles in Phases : Robots seamlessly integrate into diverse phases of industrial chemical production, from mixing and blending to packing, testing, material handling, transportation, and logistics.
- Aerial Safety Inspections : Robotic drones equipped with sensors and cameras take on the role of aerial safety inspections in chemical plants, eliminating the need for plant shutdowns or stack cooling. This innovation ensures regular plant functioning remains uninterrupted.
- Chemical Tank Cleaning Revolution : Remote-controlled robots redefine the hazardous task of chemical tank cleaning. Traditionally risky and time-consuming for human workers wearing complete personal protective equipment (PPE), the introduction of robots makes the process more efficient, safer, and devoid of production disruptions.
- Guardians in Sensitive Zones : Robots, armed with adjustable sensors and thermal imaging cameras, strategically placed in sensitive areas of chemical plants.
- Proactive Hazard Detection : Advanced sensors enable these robotic guardians to detect subtle temperature changes, signaling potential dangers before they escalate.
- Alert Mechanism : In the event of a rise in environmental temperature, robots promptly alert employees, acting as a proactive safety measure against potential fire or explosion risks.
- Fusion of Technology and Safety : Beyond machinery, these robots embody a fusion of technology and safety, actively participating in risk prevention and ensuring the well-being of the industrial ecosystem.
Main Industries that Utilize Robots in Chemical Production
Revolutionizing Precision in Fertilizer Production
- Industry Vanguard : Pioneering the way in the fertilizer industry, leading companies have seamlessly integrated robots into their operations. The intricacies of chemical mixing, vital for fertilizer production, demand a level of precision and accuracy that robots effortlessly deliver.
- Automated Mixing Precision : Robots take center stage in automating the mixing process, a critical step ensuring the meticulous proportions of chemicals are consistently maintained. This not only elevates efficiency but becomes a linchpin in reducing waste, ultimately saving costs for manufacturers in the competitive fertilizer landscape.
Pharmaceutical Innovation:
- Severe Quality Control : In the medical industry, where safety and usefulness are non-negotiable, major companies are rotating to robotics for automation in production. This strategic integration is a safeguard against errors and inconsistencies, ultimately enhancing the overall quality of drugs produced.
- Multi-faceted Robotic Applications : Beyond production automation, robots play pivotal roles in pharmaceutical processes. From filling capsules to inspecting vials for defects and packaging drugs, robots become versatile allies in maintaining the highest standards of drug manufacturing.
Democratizing Robotics in the Chemical Landscape
Beyond Corporate Giants : The grip of robotics is not a limited affair for industry giants alone. Advancements in robotics research have steered in a time where even small and medium-sized creativities (SMEs) can afford and attach the power of advanced robots. This democratization of technology ensures that innovation and efficiency are not confined to the behemoths but are accessible to a broader spectrum of players in the chemical industry.
Future Trajectory in Industrial Chemical Production
- Evolving Trends : The incorporation of robots into industrial chemical production stands as a burgeoning trend, poised to unfurl even further with the continuous evolution of robotics technology. This trajectory foresees a future where innovation becomes synonymous with efficiency, safety, and heightened quality control.
- Duality of Benefits and Challenges : The symbiotic relationship between robots and chemical production offers a spectrum of advantages – from heightened efficiency to an elevated standard of safety and quality control. Yet, within this futuristic tableau, challenges emerge. The substantial investment required and the demand for specialized skills and knowledge present hurdles in the widespread adoption of robotic systems.
- Cost Dynamics on the Horizon : Despite these challenges, the winds of change are blowing. As technology continues its relentless evolution, the anticipated decrease in implementation costs becomes a beacon of hope. This shift in cost dynamics holds the promise of democratizing access to robotic innovation, extending its reach beyond industry titans to embrace small and medium-sized enterprises (SMEs).
In the kaleidoscope of future prospects, the narrative unfolds with a delicate balance between challenges and promises, crafting a dynamic landscape where the integration of Robotics in Chemical Industry emerges as a pivotal force steering the industry towards innovation and accessibility.