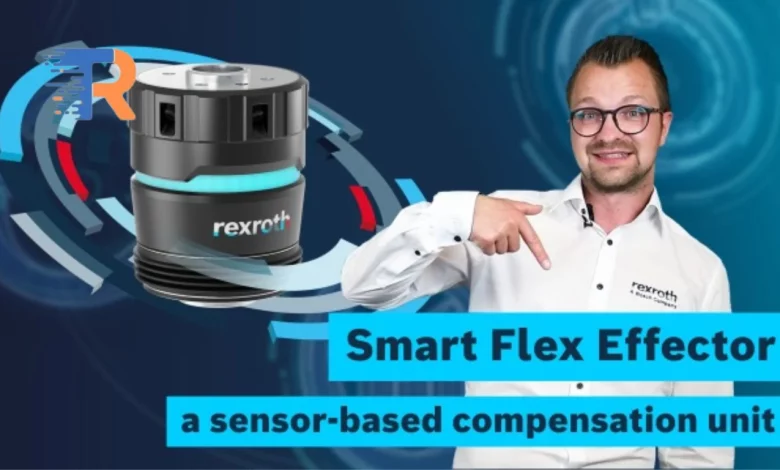
In the ever-evolving symphony of robotics, the year 2022 marked a crescendo with a remarkable 3.9 million operational robots orchestrating tasks globally, as revealed by the International Federation of Robotics. Smart Flex Effector
Envisioning a future where innovation propels robots to master an even broader spectrum of tasks, Bosch Rexroth, hailing from Buchanan, Michigan, emerges as a virtuoso in this trans-formative era.
The company, specializing in crafting intelligent systems for factory automation, mobile applications, machining, and engineering, takes center stage with the unveiling of the Smart Flex Effector a groundbreaking opus designed to elevate the flexibility and user-friendliness of robots.
Harmonizing Robotics Flexibility:
- Offering a melodic insight into the future of robotics, Brad Klippstein, a virtuoso product manager at Bosch Rexroth, emphasizes the essential need for heightened flexibility and ease of use.
- The Smart Flex Effector emerges as a transformative composition, redefining how robots interact with their surroundings by endowing them with the ability to sense object contact and optimize positioning for seamless object manipulation.
- As the global symphony of operational robots reaches unprecedented heights, Bosch Rexroth steps up to the podium with the Smart Flex Effector, positioning it strategically between the robot and its gripper to introduce a tactile feedback system that enriches the overall robotic symphony.
The Sonic Revolution of Tactile Sensing:
- The Smart Flex Effector introduces a revolutionary cadence by infusing tactile sensing into the robotic symphony. Brad Klippstein, orchestrating this symphony, highlights the monumental significance of this advancement, expressing, “We’ve had vision systems for robotics for many years.
- Now, we’re adding tactile sensing to that process to increase accuracy, repeatability, and process transparency, allowing robots to perform operations that were once considered incredibly difficult or impossible.”
- Tactile feedback becomes the resonant note, imparting robots with an elevated level of awareness, allowing them to traverse intricate tasks with unparalleled precision and fluidity.
Read Must: Robotic Arms, FAULHABER says
Amplifying Precision and Transparency:
- The incorporation of tactile sensing into the harmonious robotic composition translates into a sublime enhancement of accuracy and repeatability.
- The Smart Flex Effector becomes the virtuoso, empowering robots not just to visualize their environment through vision systems but to feel and respond to physical interactions.
- Industries immersed in the automation symphony stand to gain from heightened efficiency and a greater degree of process transparency.
- This not only broadens the spectrum of tasks robots can perform but also orchestrates a level of precision once considered elusive.
Conquering Uncharted Crescendos:
- Bosch Rexroth’s Smart Flex Effector boldly conducts the robotic symphony, conquering challenges posed by operations deemed difficult or impossible before.
- This groundbreaking composition heralds a new movement, redefining the limits of what robots can achieve in manufacturing, engineering, and various industries.
- By enabling robots to sense and respond to their surroundings on a tactile level, the Smart Flex Effector becomes the maestro opening unexplored harmonies for automation, making tasks once considered beyond robotic capabilities now within reach.
Propelling the Future Crescendo of Robotics:
- As Bosch Rexroth propels the industry forward with the Smart Flex Effector, the future of robotics takes center stage as a dynamic and adaptable symphony.
- The continuous evolution of intelligent systems positions the Smart Flex Effector as the virtuoso, setting the stage for an era where robots seamlessly traverse complex tasks with precision and agility.
- This integration of tactile sensing becomes not just a technological milestone but a resounding moment in enhancing the collaborative capabilities of robots and humans, composing an automation symphony that resonates with accessibility and impact.
Bosch Rexroth makes industrial arms more flexible Smart Flex Effector
Industrial robots, especially the big ones, often struggle with flexibility and learning new tasks easily.
Bosch Rexroth acknowledges this hurdle, pointing out that those traditional robots in picking processes rely on fixed “teach positions.” Unfortunately, these positions can pose problems when faced with slight variations in the item or the robot’s placement.
- Smart Flex Effector: Adding a Touch of Flexibility
- Brad Klippstein, a key player at Bosch Rexroth, sheds light on how the Smart Flex Effector tackles these challenges by introducing a touch-based approach.
- Unlike the conventional need for precise information about an object’s exact position, this smart solution allows for a more intuitive interaction.
- Klippstein explains, “I can get somewhat close and then have the Smart Flex Effector tell me exactly where to go based on tactile sensing or touch.”
The Power of a Touch:
- While vision systems are crucial for robot feedback, Bosch Rexroth emphasizes the unique advantage of incorporating tactile feedback.
- This means that as soon as the robot makes contact with the workpiece, it instantly “feels” the environment, providing immediate insights into its positioning.
- This touch-based feedback proves particularly valuable in scenarios where pinpoint accuracy may not be necessary.
Flexibility without the Learning Curve:
One standout feature of the Smart Flex Effector is its ability to introduce flexibility without the constant need for retraining. Klippstein points out, “With all of these teach positions, we can get somewhat close, and the Smart Flex Effector adds flexibility to that process so that you don’t have to reteach that position each time.” This simplicity becomes essential in dynamic industrial settings where tasks and positions may vary.
Precision Tweaking with Instant Information:
Taking simplicity a step further, the Smart Flex Effector allows for precise corrections by offering immediate information about any deviations in position. Klippstein illustrates, “If we know that the position is off half a millimeter in the X direction, three-quarters of a millimeter in the Y direction, and 2.5 degrees about the X-Y axis, and we know all of those dimensions immediately, we can send that information back to the robot. Then it knows the exact position to correct.”
- Bosch Rexroth’s Smart Flex Effector emerges as a game-changer in the world of industrial robotics.
- By simplifying the challenges of inflexibility and eliminating the need for constant reteaching, this innovation adds a touch of adaptability to large industrial robots.
- The introduction of touch-based sensing not only provides a new level of flexibility but also streamlines precision adjustments, making the Smart Flex Effector a pivotal step forward in the evolution of industrial automation.
- As industries strive for simplicity, efficiency, and agility, Bosch Rexroth’s inventive solution sets the stage for a more responsive and user-friendly future in industrial robotics.
Unlocking the potential of robots in various industries necessitates a keen focus on flexibility and seamless integration. With the increasing prevalence of robotics, adaptability and ease of implementation have become critical aspects of industry discussions.
Brad Klippstein, shedding light on current trends, emphasizes the importance of making end effectors effortlessly compatible with a range of robots chosen by customers. Simplifying the communication process and ensuring easy programming from the teach pendant are pivotal trends, enabling the swift implementation of solutions.
Klippstein highlights that recent strides in artificial intelligence contribute to the continuous improvement of end-of-arm tooling, such as the Smart Flex Effector, enhancing accuracy over time.
The wealth of information provided by these advancements empowers users to gain insights into ongoing processes, enabling efficient programming adjustments or the exploration of innovative ways to implement solutions across various domains.