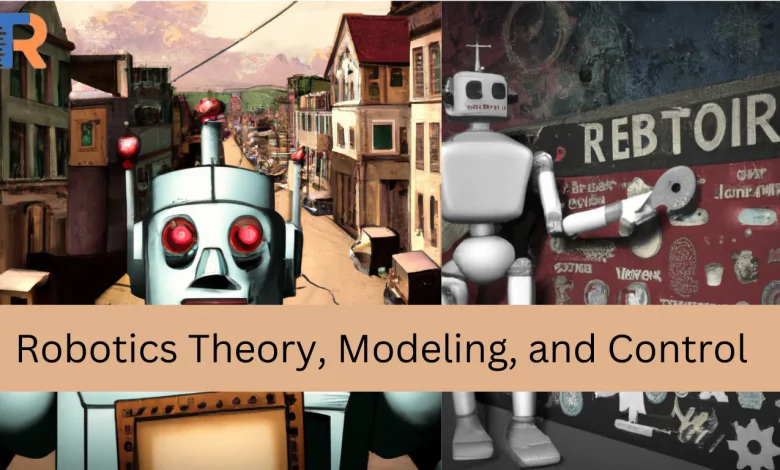
In the ever-evolving landscape of technology, the integration of industrial robotics has become a driving force behind the optimization and transformation of various industries. At the heart of this revolution lies the intricate interplay of industrial robotics theory, modeling, and control. This article delves into the depths of these concepts, shedding light on their significance and unraveling the complexities that make industrial robots the backbone of modern manufacturing processes.
Industrial Robotics Theory Modeling
Before delving into the realms of control, it is crucial to understand the theoretical underpinnings that guide the design and development of industrial robots. The realm of industrial robotics theory modeling is a multidisciplinary field that draws upon principles from mechanical engineering, electrical engineering, computer science, and control theory. At its core, it seeks to create mathematical models that capture the dynamics and behavior of robotic systems.
One key aspect of industrial robotics theory modeling is the representation of the robot’s physical structure and its interactions with the environment. This involves formulating equations that describe the robot’s kinematics and dynamics, allowing engineers to predict its motion and response to external forces accurately. This theoretical foundation serves as the cornerstone for the subsequent stages of development, including control system design.
Control Theory in Robotics
Control theory in the context of robotics is the art and science of manipulating the behavior of a robot to achieve desired outcomes. At the heart of this discipline is the concept of a control system, a sophisticated mechanism that governs the robot’s movements and actions. This system relies on feedback mechanisms to continually adjust the robot’s behavior based on the difference between the desired and actual outcomes.
In the realm of industrial robotics theory modeling, the control system plays a pivotal role in ensuring precision, accuracy, and adaptability. It encompasses a set of algorithms and protocols designed to guide the robot through its tasks with efficiency. Proportional-Integral-Derivative (PID) controllers, state-space models, and adaptive control are just a few examples of the sophisticated techniques employed in crafting control systems for industrial robots.
Control System on an Industrial Robot
The control system on an industrial robot is akin to the robot’s central nervous system, orchestrating a symphony of movements and actions with unparalleled precision. At its core, this system receives sensory input from various sources, processes the information, and generates commands to drive the robot’s actuators. The feedback loop is a critical component, allowing the control system to continuously refine and optimize the robot’s performance.
Industrial robots are endowed with an array of sensors, such as encoders, cameras, and force/torque sensors, which feed real-time data to the control system. The control algorithm interprets this information and adjusts the robot’s trajectory, speed, and force application accordingly. This closed-loop system ensures that the robot can adapt to dynamic environments and unforeseen challenges, making it an invaluable asset in complex manufacturing scenarios.
Why Industrial Robots are Important
The importance of industrial robots in modern manufacturing cannot be overstated. These sophisticated machines have revolutionized the production landscape, offering unprecedented levels of efficiency, precision, and versatility. The integration of industrial robots leads to increased productivity, reduced costs, and enhanced product quality, ultimately contributing to the competitiveness and sustainability of industries.
One of the primary advantages of industrial robots lies in their ability to perform repetitive and labor-intensive tasks with unwavering accuracy. This not only minimizes the risk of human error but also frees up human workers to focus on more complex and cognitive aspects of production. Moreover, industrial robots can operate in hazardous environments, mitigating risks to human safety.
The Three Main Parts of an Industrial Robot
To comprehend the inner workings of an industrial robot, it is essential to break down its structure into three main components: the manipulator, the controller, and the end effector.
- Manipulator:
The manipulator is the mechanical arm of the industrial robot responsible for executing tasks. Comprising joints and links, the manipulator mimics the dexterity of the human arm, allowing the robot to reach, grasp, and manipulate objects. The design of the manipulator is intricately linked to the robot’s range of motion, payload capacity, and overall versatility.
- Controller:
The controller serves as the brain of the industrial robot, housing the control system that governs its movements. It processes input from sensors, computes the necessary adjustments, and sends commands to the robot’s actuators. The sophistication of the controller determines the robot’s responsiveness, accuracy, and adaptability, making it a critical element in the overall functionality of the system.
- End Effector:
The end effector is the business end of the industrial robot, the tool or device attached to the manipulator for interacting with the environment. This could be a gripper for picking up objects, a welding torch for joining materials, or a cutting tool for precision machining. The choice of the end effector depends on the specific tasks the robot is designed to perform, making it a customizable component tailored to the needs of the application.
Conclusion
In the realm of modern manufacturing, the synergy between industrial robotics theory modeling and control is reshaping industries and pushing the boundaries of what is possible. The meticulous design of control systems, informed by sophisticated theoretical models, empowers industrial robots to navigate complex tasks with grace and precision. As we embrace the era of Industry 4.0, the importance of industrial robots in enhancing efficiency, ensuring safety, and driving innovation cannot be overstated. Industrial robotics theory modeling is not just a concept; it’s a catalyst for transformative change, heralding a future where automation and human ingenuity coexist in perfect harmony.
Understanding the Essence: Kinematics and Dynamics in Industrial Robotics Theory Modeling
In the intricate realm of industrial robotics theory modeling, two fundamental concepts, kinematics, and dynamics, serve as the bedrock for designing robots that move with precision, accuracy, and efficiency. These concepts not only define the physical behavior of robots but also pave the way for the development of control systems that orchestrate their movements in complex industrial environments.
Kinematics: Deciphering Motion
The Essence of Kinematics
Kinematics is the branch of robotics theory modeling that delves into the study of motion without concern for the forces that cause it. It seeks to answer questions related to the position, velocity, and acceleration of different parts of a robot as it moves through its workspace. In simpler terms, kinematics deals with the “how” of motion, offering insights into the spatial relationships between various components of a robot.
Types of Kinematics in Industrial Robotics
In the context of industrial robotics, there are primarily two types of kinematics: forward kinematics and inverse kinematics.
- Forward Kinematics:
Forward kinematics involves determining the end-effector’s position and orientation based on the joint angles and lengths of a robot’s manipulator. This process is akin to plotting the trajectory of the tip of the robot’s arm without considering the forces acting on it. Through forward kinematics, engineers can precisely predict where the robot’s end effector will be located in its workspace for a given set of joint angles.
Example: If we know the joint angles of a robot arm, forward kinematics can help us calculate the position and orientation of the gripper at the end of the arm.
- Inverse Kinematics:
Inverse kinematics, on the other hand, addresses the challenge of determining the joint angles required to position the end-effector at a specific location and orientation. It’s the reverse process of forward kinematics, focusing on understanding how to manipulate the joints to achieve a desired spatial configuration of the robot.
Example: Given a target position for the robot’s gripper, inverse kinematics can help calculate the joint angles needed to reach that position.
Dynamics: Unraveling Forces and Motion
The Essence of Dynamics
While kinematics focuses on describing motion, dynamics takes the analysis a step further by considering the forces and torques that drive that motion. In other words, dynamics in industrial robotics theory modeling aims to understand how the robot’s motion is influenced by external forces, gravity, and the inertial properties of its components.
Types of Dynamics in Industrial Robotics
- Forward Dynamics:
Forward dynamics involves predicting the motion of a robot’s components based on the forces and torques applied to it. This is particularly crucial in scenarios where understanding how a robot responds to external influences is essential. Engineers employ complex mathematical models to simulate the dynamic behavior of the robot and predict its motion under different conditions.
Example: If a force is applied to a robot arm, forward dynamics can help predict how the arm will move in response to that force.
- Inverse Dynamics:
Inverse dynamics is concerned with determining the forces and torques required at each joint to produce a desired motion. This is particularly valuable for designing control systems that can exert the necessary forces to achieve precise and controlled movements.
Example: If we want a robot to follow a specific trajectory, inverse dynamics can help calculate the forces needed at each joint to achieve that trajectory.
Bridging Kinematics and Dynamics in Industrial Robotics
In the context of industrial robotics theory modeling, kinematics and dynamics work hand in hand to provide a holistic understanding of a robot’s motion. While kinematics sets the stage by defining how a robot moves through its workspace, dynamics adds the crucial layer of understanding the forces and torques involved in that motion.
For engineers and roboticists, the integration of kinematics and dynamics is pivotal in creating accurate models that not only predict a robot’s behavior but also inform the design of control systems. This synergy ensures that the control algorithms can account for the physical constraints and dynamics of the robot, leading to more precise and efficient control of its movements.
Conclusion: The Symphony of Motion
In the grand symphony of industrial robotics theory, kinematics and dynamics play the roles of composers, shaping the intricate dance of machines in the modern manufacturing landscape. Understanding how robots move and respond to external forces is not merely an academic pursuit but a practical necessity for designing robots that can navigate the complexities of real-world industrial applications.
As we delve deeper into the realms of industrial robotics theory modeling, the harmonious integration of kinematics and dynamics becomes the key to unlocking new frontiers in automation. From predicting a robot’s precise trajectory to calculating the forces required for optimal performance, the marriage of kinematics and dynamics propels industrial robotics into a future where machines move with unparalleled precision and grace.