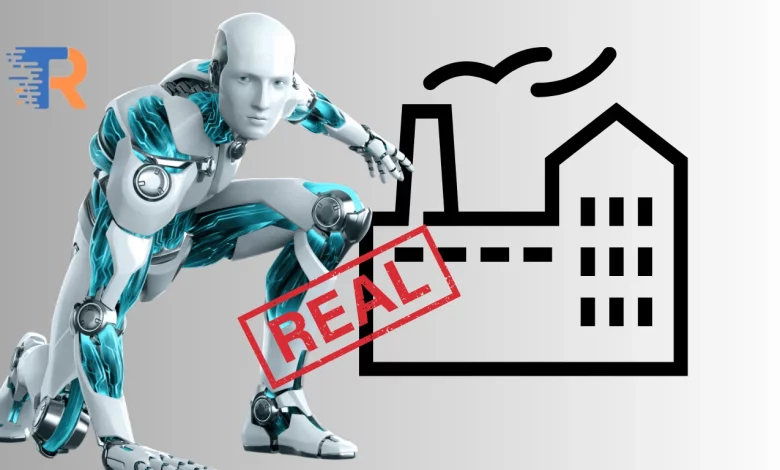
A discordant note has been struck in the supply chain by a symphony of obstacles in the dynamic world of plastic and Robotics in the Rubber Industry, which has forced producers to look for harmonic solutions. A complicated web of difficult-to-untangle hurdles faces the business as a result of the current lack of natural rubber and the catastrophic effects of winter storm Uri in Texas, a major hub for the manufacture of plastic resin and Robotics in the Rubber Industry.
The COVID-19 pandemic’s worldwide demand for medical supplies led to a boom in the market for plastic and rubber components, forcing producers to balance growing demand with a narrow supply line.. Instead of being brief interruptions, the effects had a long-lasting ripple effect that affected every aspect of the manufacturing environment.
In the face of this intricate scenario, manufacturers are turning to technological sentinels – robots. These automated virtuosos are emerging as essential tools to navigate the intricacies of supply chain disruptions. With the scarcity of natural rubber and logistical impediments, companies are seeking inventive avenues to augment productivity and efficiency, with robotics leading the charge in this transformative odyssey.
- The winter storm Uri, temporarily incapacitating resin refineries in Texas, served as a clarion call for the industry. Manufacturers discerned the imperative need for resilient solutions to mitigate risks and disruptions. The rise in demand for medical supplies, including latex gloves, highlighted how critical it is to quickly adjust to changing market conditions.
- When faced with the choice of keeping rising expenses or passing them on to customers, manufacturers are using automation as a third option. The integration of robotics not only amplifies production output but also presents an opportunity to diminish reliance on manual labor, effectively addressing the challenge of surging demand without compromising competitiveness.
- Embarking on an exploration of robotics in plastics and rubber manufacturing unveils a panorama of inventive solutions. From automated assembly lines orchestrating a seamless ballet of production to robotic arms delicately handling intricate tasks, the industry is witnessing a transformative shift towards a future where human-machine collaboration is intrinsic to success.
This exploration will unravel the diverse facets of how robots and automation are evolving into indispensable allies for manufacturers striving not only to weather the tempests of supply chain disruptions but also to emerge as more resilient, agile, and fiercely competitive players in an ever-evolving market symphony.
Injection Molding – Machine Tending
Injection molding, a cornerstone of modern manufacturing, finds its dynamic counterpart in the realm of robotic machine tending. The orchestration of robots in this process often takes the form of Cartesian precision, aligning seamlessly with the geometric intricacies of molding machines to deftly extract finished parts.
- However, the dance of innovation doesn’t stop there. Manufacturers, in their quest for versatility, frequently opt for the prowess of six-axis articulated arms in tandem with injection molding machines. These articulated marvels, with their flexibility akin to a virtuoso’s performance, transcend the boundaries of conventional rigidity and unlock the potential to execute a myriad of functions with finesse.
- Yet, the symphony of automation doesn’t merely play a singular note. In a harmonious fusion, a combination of robots takes center stage. Picture the Cartesian virtuoso delicately plucking a finished part from the molding machine, seamlessly passing the baton to a six-axis articulated accomplice. This dynamic duo unfolds a narrative of efficiency, where the Cartesian precision sets the stage, and the articulated finesse adds layers of intricate operations to the manufacturing ballet.
This intersection of robotic ballet and molding artistry not only exemplifies the adaptability of modern manufacturing but also underscores the transformative power of collaboration between distinct robotic entities. It’s a tale of precision and flexibility converging on the factory floor, shaping the future of injection molding with a fresh choreography that echoes the symphony of progress in every finished piece.
Trimming and Removing Excess Material
In the intricate ballet of injection molding, the crucial act of trimming and removing excess material takes center stage. As a necessary choreography in the manufacturing process, the choice between a blade cutter and a spindle armed with a grinding tool depends on the material’s pliability. A blade cutter gracefully dances through pliable material, while the unyielding grasp of a spindle and grinding tool is reserved for hardened substances. In both scenarios, the choreographer is a robotic virtuoso wielding the appropriate End-of-Arm-Tooling to execute the job with precision and finesse.
- The decision to enlist a robot for the delicate task of material removal after molding is not arbitrary; it’s a conscious move towards achieving elevated quality and unwavering consistency. In this dance of automation, the robot becomes the guardian of excellence, surpassing the capabilities of manual methods.
- Beyond the realms of precision and consistency, the inclusion of robots in this process acts as a shield against potential hazards. The repetitive nature of injection molding and manual part removal is a breeding ground for workplace injuries. The risk of crushing injuries and amputations looms when hands or limbs find their way between the halves of a mold. According to the US Bureau of Labor Statistics, workplace injuries extract a staggering cost of $1 billion per week. The deployment of robotics becomes not just a choice for efficiency but a commitment to keeping human operators safer.
The advantages of embracing robots extend beyond safety. Unburdened by fatigue or the need for breaks, these tireless automatons empower manufacturers to amplify output in injection molding operations. This not only translates into increased productivity but liberates human associates from the shackles of dangerous and monotonous tasks. Robotics in the Rubber Industry ,they are then free to engage in more intellectually stimulating and high-value endeavors, forging a narrative of innovation and progress on the factory floor.
Quality Control/Inspection Robotics in the Rubber Industry
In the intricate tapestry of manufacturing, the quest for quality control and inspection unfolds as a pivotal act. Enter the virtuosity of machine vision systems, the unsung heroes that tirelessly scrutinize the nuances of plastic and rubber parts in Robotics in the Rubber Industry. Robots, adorned with the mantle of computer vision, extend their discerning gaze across a spectrum of processing methods – from the rhythmic cadence of injection molding to the dynamic twirls of rotational molding, the precision of extrusion, the compression ballet, and beyond.
- Yet, even in this dance of precision, challenges emerge. The gleaming surfaces of certain materials, akin to unruly performers in the spotlight, sometimes defy the efficacy of computer vision inspections. Reflections, akin to a deceptive pirouette, can be misconstrued as imperfections. Here, the stage is set for autonomous machine vision to take charge, orchestrating the optimal angle and lighting to gracefully sweep away errors, ensuring a flawless performance.
- In the ballet of quality control, physical measurements also take their turn in the limelight. Calipers, depth gauges, and an array of specialized End-of-Arm-Tooling become the instruments of meticulous measurement, each note played with the precision of a seasoned maestro.
- The automation of quality inspection isn’t merely a technical marvel; it’s a transformative act that elevates traceability to an art form. Every stroke of the robotic inspection brush adds layers of accountability, contributing to an ensemble that strives for nothing short of excellence. It’s a symphony where each automated inspection enhances not only the efficiency of the process but also the very essence of the finished product.
As the curtain falls on the ballet of quality control, the resonance lingers. The marriage of robots and machine vision in this performance isn’t just a choreographed routine; it’s an ode to precision, an anthem of flawless execution, and a testament to the relentless pursuit of perfection on the manufacturing stage.
Navigating the landscape of Robotics in the rubber industry, even with a clear vision of your requirements, can be a time-consuming quest for identifying qualified vendors. The solution lies in leveraging the unparalleled resources of the world’s largest directory of robot vendors, ensuring a seamless match with companies possessing the expertise tailored to your needs. In this technological journey, Technology Refers emerges as a guiding beacon, streamlining the process of obtaining multiple quotes through a well-orchestrated and planned approach. With four simple steps, from defining your needs to receiving offers, Technology Refers transforms the vendor discovery and selection process, making it an efficient and effective venture in the dynamic realm of Robotics in the rubber industry.